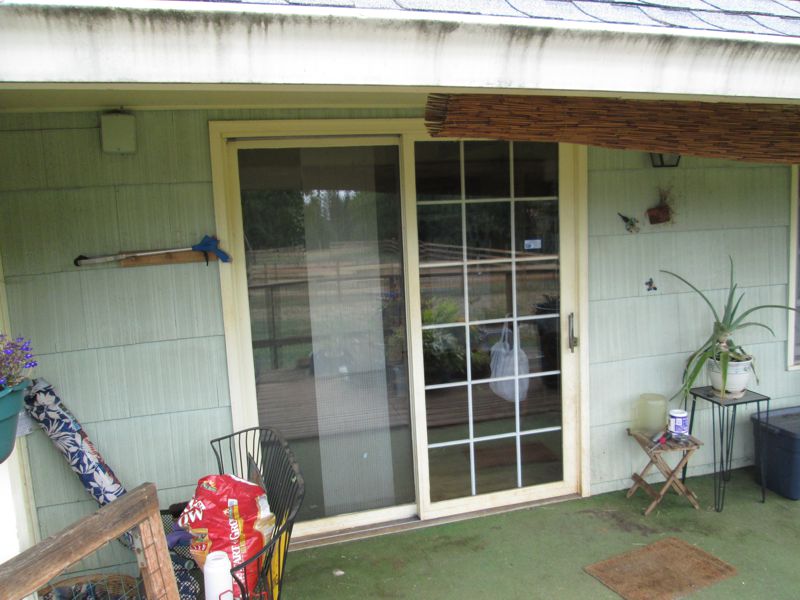
Your stereotypical Pella wood sliding patio door, needs the inevitable roller-replacement that comes with years of use.
|
But there is nothing typical about removing the original roller chassis.
|
Finding what looks like screws coming down from ABOVE the roller-chassis, we begin disassembly of the door rail from above the rollers.
|
Sure enough, there’s one of the screw-heads right there between the top of the bottom-rail, and the insulated glass unit. Certainly not something you see every day. (You may need to enlarge the photo to see the screw.)
|
And so, since the insulated glass unit is going to have to be temporarily removed, we go about removing all the overlapping wood-sticking that holds the glass to the door.
|
This photo shows you the one-piece METAL sub-structure Pella uses (see RED arrows) to hold the primary stile & rail components together, which unintentionally prevents the simple removal of just the bottom-rail, because the screws go through this substructure from the glass side. Thus, the glass must be removed before you can access the screws that hold the bottom-rail (and the other components) in place. Pella’s engineers did not seem to be giving much thought here, to the maintenance headaches they were creating down the road for those who would eventually need to replace the rollers.
|
Our own solution to future maintenance needs down the road for this door, was to replace the original “single-roller-type” of roller with a “tandem-set of rollers” that could be “surface-mounted” to the bottom of the door. If you enlarge the photo, you’ll get a better idea of what we’re talking about.
|
This will facilitate someone only having to lift the door out of the jamb assembly to replace the rollers next time. Although, these tandem-rollers will probably outlive the door assembly.
|
The wood-stops are reinstalled with screws, to replace the nails Pella used originally (See Photo #5).
|
We would want to go on record as saying that Pella makes a top-shelf product. Certainly as good as any of the other major wood-window & door manufacturing contenders. They’ve all had their issues over the years, and most of them have learned to improve their products over time. Learning from their mistakes, as do most all of us.
|
|
|