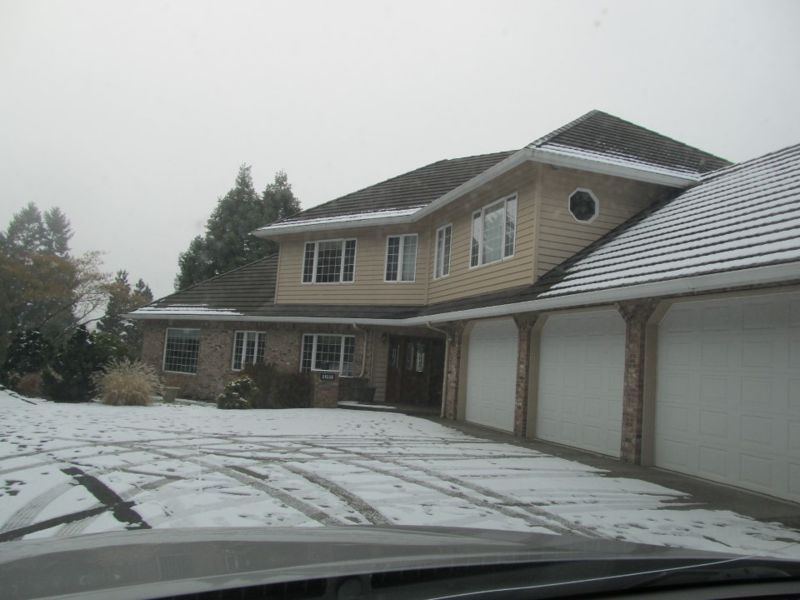
Late fall 2013, just West of Vancouver Washington. A very light dusting of snow was received the day we went out to look at this project.
|
But as is often the case in the
Willamette Valley, it didn’t last. The glass in two large vinyl picture windows in the family room have failed (fogged-up).
|
This is one of those homes with a daylight basement that faces out the back. So even though the windows are on the main floor relative to the front of the house, they sit above the basement on the back side, creating the logistics of a 2nd story opening.
|
Fortunately, we were able to park very close to the front door, so when it came time to transport the new glass, it was pretty much an adequately unobstructed path from the door, down two steps through the dining room to the two openings in the family room.
|
But first the original glass is removed from the vinyl frame to the exterior, and then due the opening being wider than it is tall, we must first tilt the glass to an appropriate angle before we can pass it back in through the opening to the interior side.
|
After which it is transported through the house, out the front door near one of our vans in preparation for it being loaded onto the van once both of the new insulated glass units has been taken in to their respective openings…
|
…as is shown being done in the above photo.
|
Here we have Gordon & Phil waiting upon Jared & Sean (see glass reflection) to complete the application of the new glazing tape to the original vinyl window frame.
|
The new glass is then carefully transported out through the opening, onto the scaffold, after which it is turned and positioned to be lifted into the original Vinyl window frame.
|