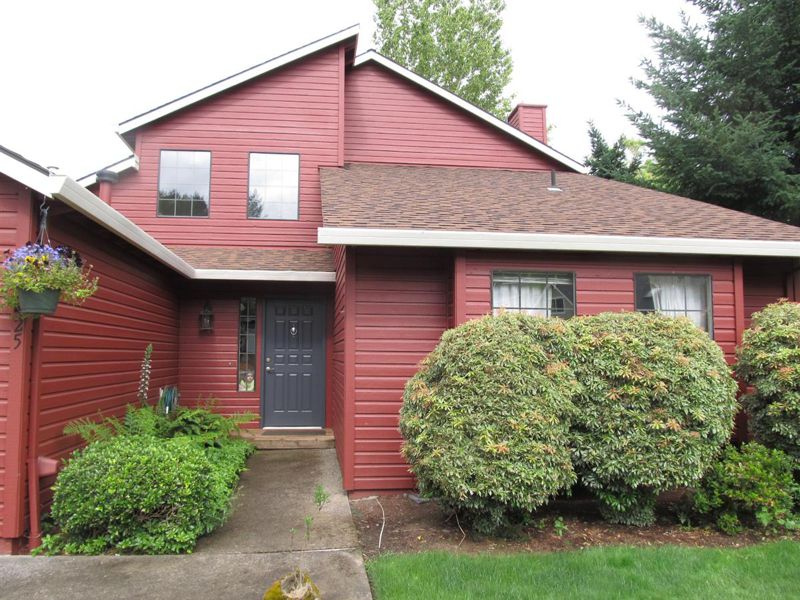
Time to upgrade those old cold, drafty, moisture condensing aluminum-framed windows.
|
Field technician David Castro goes about showing us how it’s done. Cut back the siding to make room for the composite exterior trim that not only looks nice around the new vinyl windows…
|
…but also facilitates the proper flashing of the new windows into the moisture barrier that exists beneath the siding. So the aluminum windows are then removed…
|
…and the new Mercer Vinyl windows are installed. If you look back at the first couple photos, you may be able to notice that the original windows here were non-operable picture windows, and yet the windows David is installing are single-hung windows.
|
If you enlarge the above photo by clicking on it, the INSET photo shows that these windows sit fairly high above a stairwell. So typically, there would be no reasonable way to reach operable windows. However, given the ease with which these Mercer Single-Hung windows slide up & down, we were, at our client’s bequest, able to devise an attachment on the end of a pole (doweling) that allowed the operable sash to be easily pushed up or pulled down from below if the windows were left unlatched.
|
Another requested change came in the form of wanting a little more ventilation in the master bedroom. So the former octagon-shaped picture window was changed from a non-operable opening to a crank-out awning window. Bruce is one of our drywall artisans, among many other skill-sets.
|
Brandon is shown here putting the finishing touches on the sliding patio door we replaced. What exactly is he doing? He’s tooling the caulking. Notice the paper-towel in his hand, and the blue-masking tape on the opposite side of the opening? Some folks may find it interesting to note that regardless of the technical aspects of installing a door or window correctly to ensure years of hassle-free operation and an adequate barrier against moisture infiltration into our client’s walls…it’s the “detail-work,” either good or bad, that most people will notice when a contractor is finished with a project.
|
The back of the house.
|
One of the sides.
|