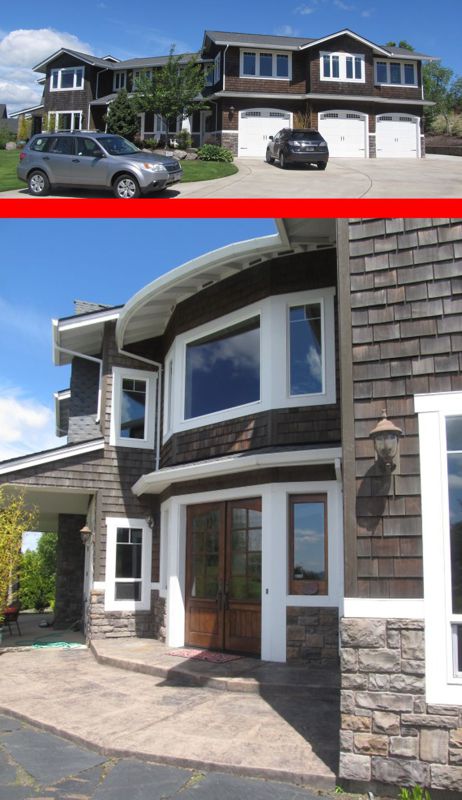
Up on the top of Cooper Mountain in Beaverton with a double-entry set of wood doors facing Southwest from whence comes all the inclement marine weather. Can you see how the shape of the house around these doors might almost scoop all the wind-driven moisture and funnel it to this door opening?
|
Nice looking doors. A slight variation on the Simpson 568 Traditional Sash Door. But well on their way to very serious problems with substantial water penetration splitting the various components and swelling up the two doors against each other so badly that you can’t get them open in the winter.
|
If you enlarge the above photo by clicking on it, you may be able to make out some of the damage in this collage of close-ups.
|
We advised our clients to install fiberglass doors here, and priced that option for the record, but they had it in mind to roll the dice a little longer with the existing doors.
|
So at their request, and a signed contract, we went about cutting out both bottom-rails, which frequently suffer the most extreme damage in these situations. Our technician Steve Hilt is shown above using his Festool saw to carefully remove one of the bottom-rails. Note the guide clamped to the door.
|
After which Steve goes about installing the new rail-components by drilling holes through the door stiles, into which some steel lag-bolts will be anchored into the new rail-material.
|
A careful color match under Steve’s artistic eye and then Jared is shown wiping off the doors before we apply one of the many coats of Spar-Urethane. All joints and remaining splits were also carefully sealed with a quality polyurethane caulking in a close-matching wood-tone color in-between the coats of sealant.
|
We underbid this one a bit. Feeling good about what these doors needed after closer scrutiny, necessitated more work than was originally planned. Steve carefully straps one of the doors to his van on the day we returned a week and a half or so after having initially retrieving them & taking them to our warehouse.
|
While Steve goes about installing an after-market interlocking aluminum threshold & threshold-pan (Pemko 145D), David Castro is nailing the corresponding Z61 zinc interlocking hooks onto the bottom of the doors. If our client is able to stay up with the maintenance by having these doors recoated every year or two…
|
…they may get another 5 to 10 years out of them. But even then it’s hard to say for certain, because it is unknown what degree to which the original components were exposed, even though they (the components) feel firm now…the rot causing organisms could potentially already be internally entrenched.
|
|
|